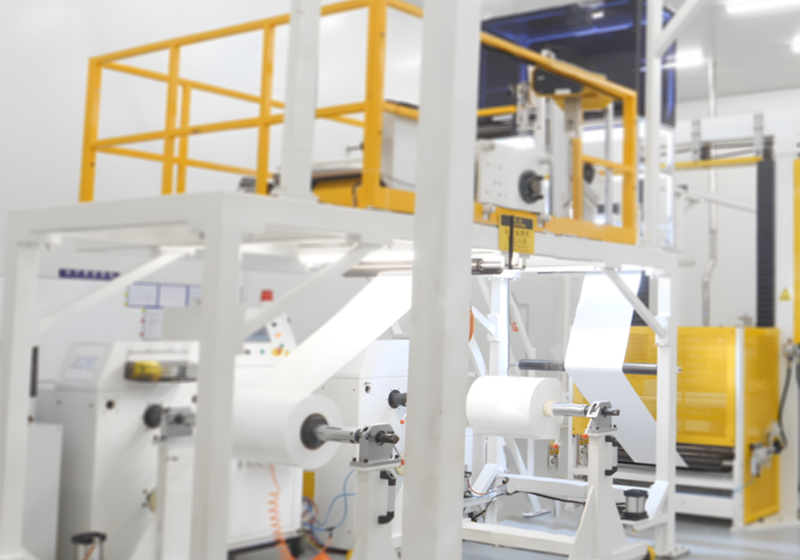
Extrusion Sheet
The process of extrusion from raw materials to sheets involves three stages: plasticization, extrusion, and shaping. The extruder and some auxiliary devices are the main equipment to complete this process.
Service Industry: Widely used in food (fast-moving consumer goods, condiments, etc.), home, personal care products, pharmaceuticals, and electronics industries.
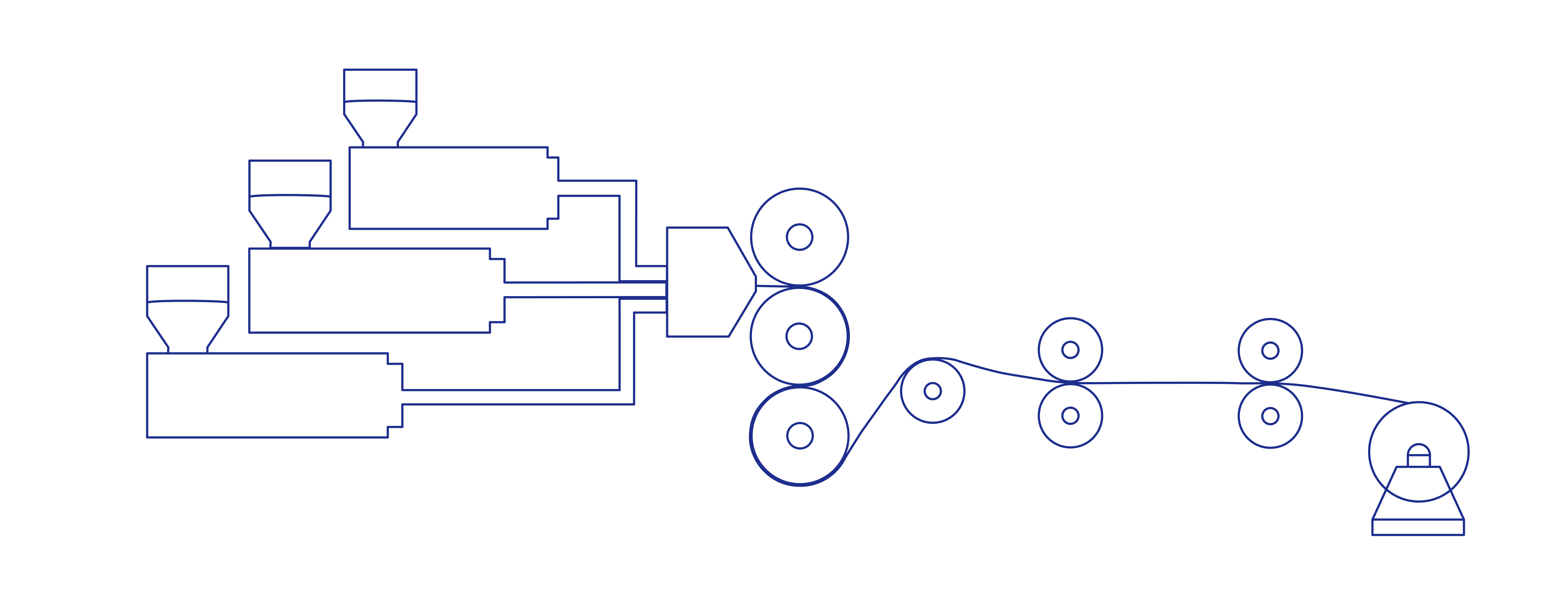
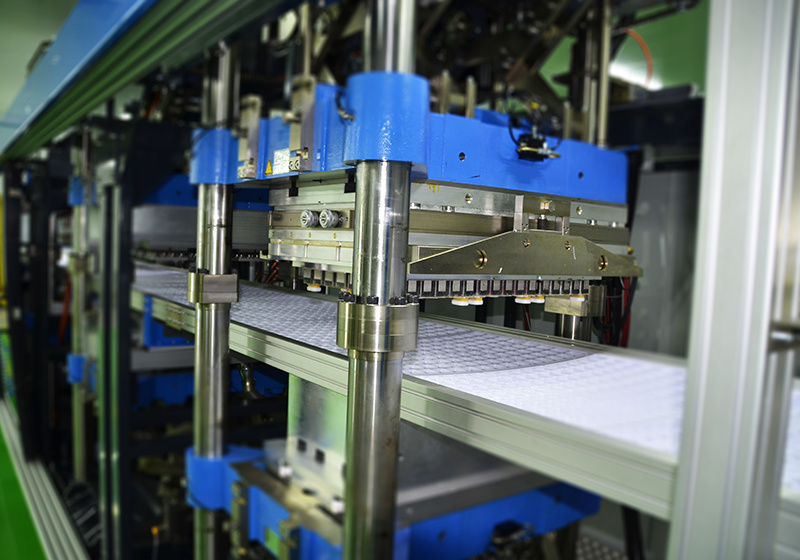
Thermoforming
The extruded sheet material is transported to the vacuum forming machine through the feeding rack and heated to a softened state. The sheet material is stretched and adhered to the mold cavity through vacuum suction, cooled and formed, demolded, punched, stacked, and packaged.
This process has the characteristics of rapid sample production and efficient production, including PP, PET, PS, PE coated blister trays, etc.
Service industries: food, electronics, fast-moving consumer goods, medical devices, and other industries.
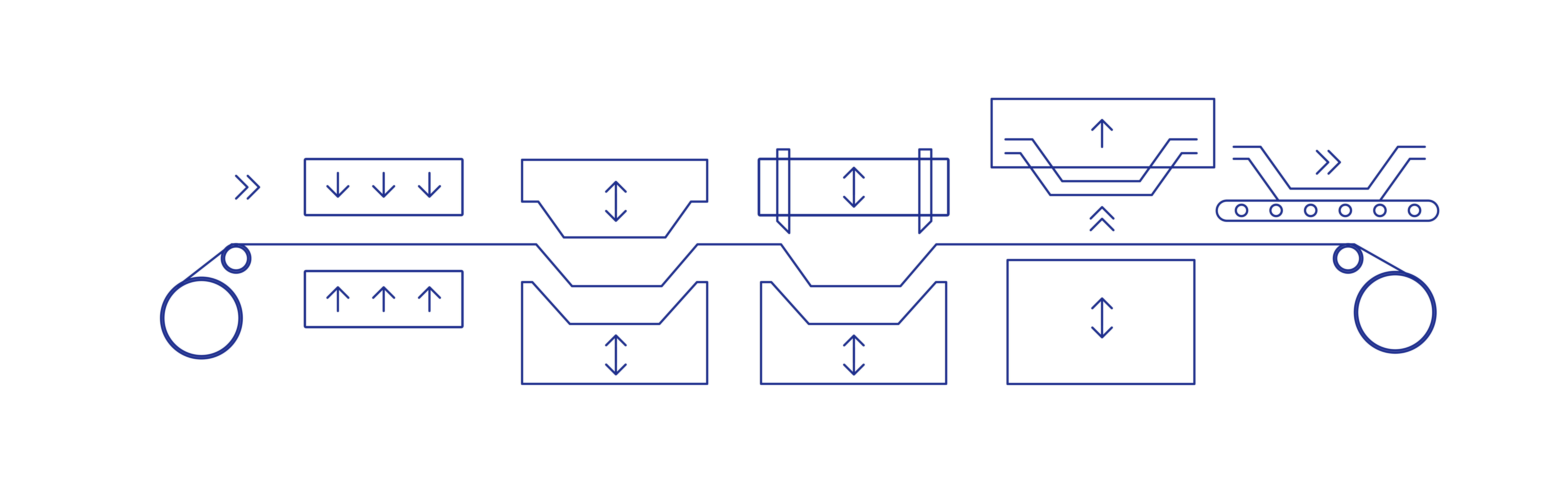
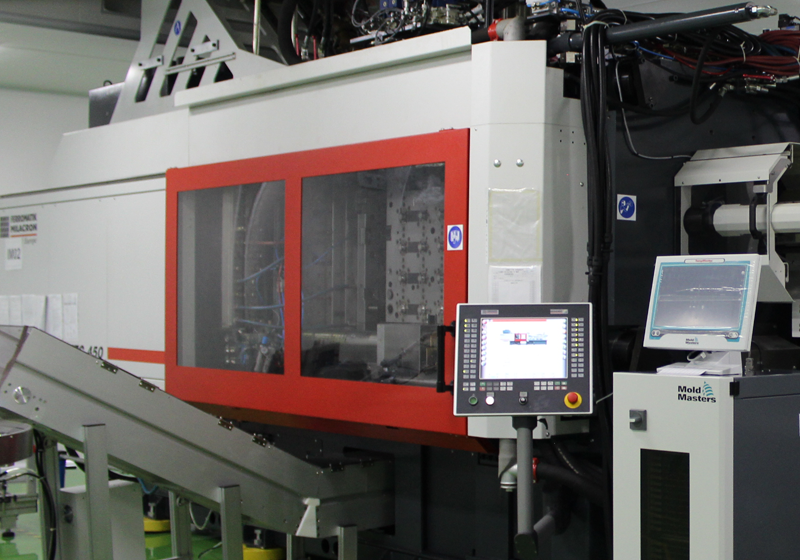
Injection Molding
At a certain temperature, by pushing the screw, the plasticized plastic melt is injected into the closed mold cavity, cooled, solidified, and shaped before demolding to obtain the product.
This method is suitable for mass production of complex shaped components, industrial accessories, or disposable consumer goods, and is one of the commonly used methods in plastic molding and processing.
Service Industry: Food, health products, electronics, fast-moving consumer goods, medical devices, pharmaceuticals, etc.
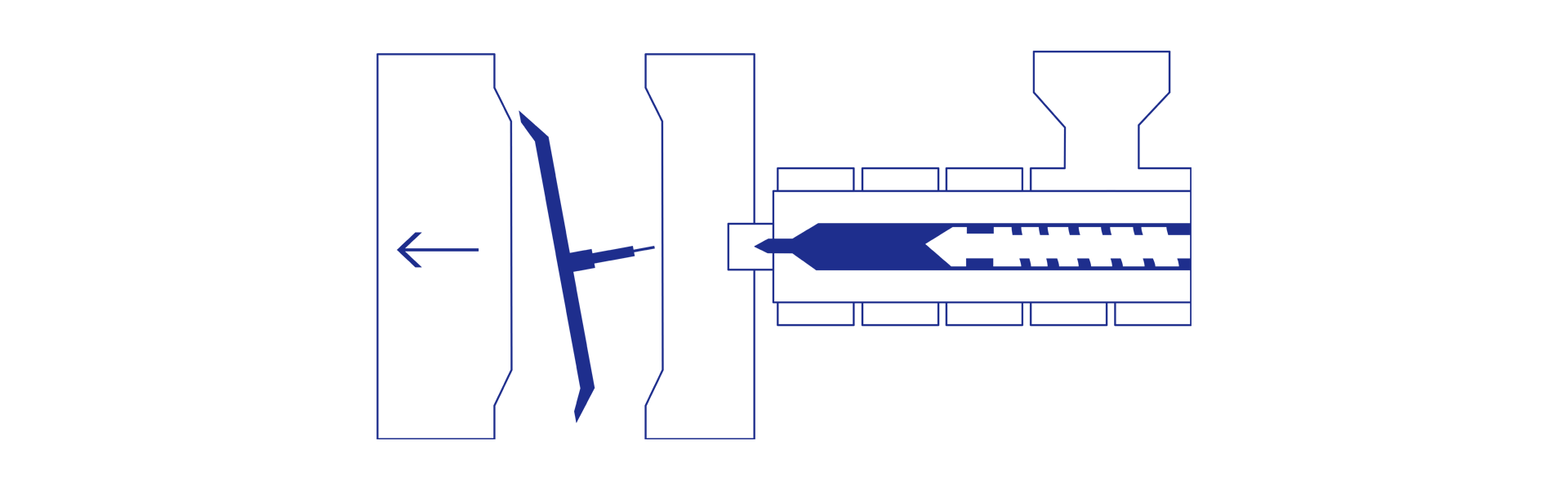
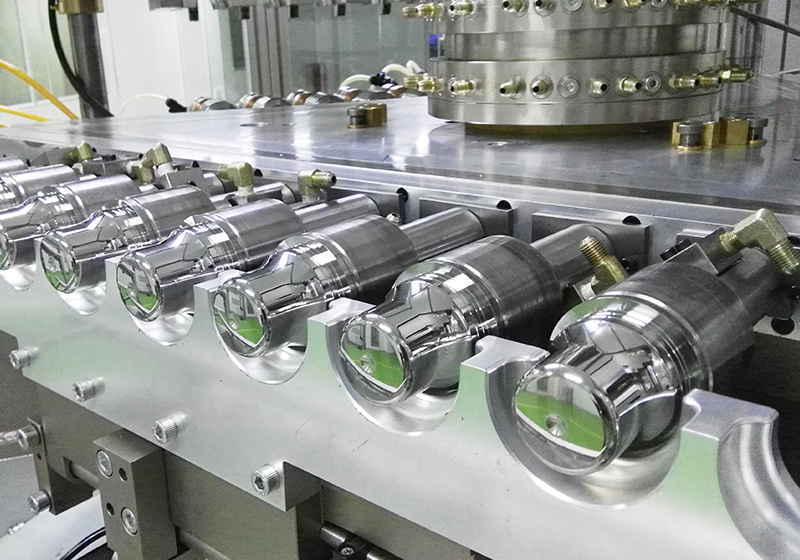
Injection Blow Molding
Firstly, plastic is injected around the preform core rod, and a hollow bottle preform with a bottom is formed by injection molding. At the same time, the temperature state of the preform is adjusted. Then, the preform is transported through the core rod to the blow molding model, and compressed air is exported from the core rod to blow molding the preform into the shape of the model. After the bottle is formed, the product can be obtained by demolding.
The injection blown process can have a good appearance and accuracy, and is mainly suitable for producing packaging containers (bottles) with small capacity, high hygiene and weight requirements.
Service Industry: Food, health products, large health categories, medical devices, pharmaceuticals, etc.
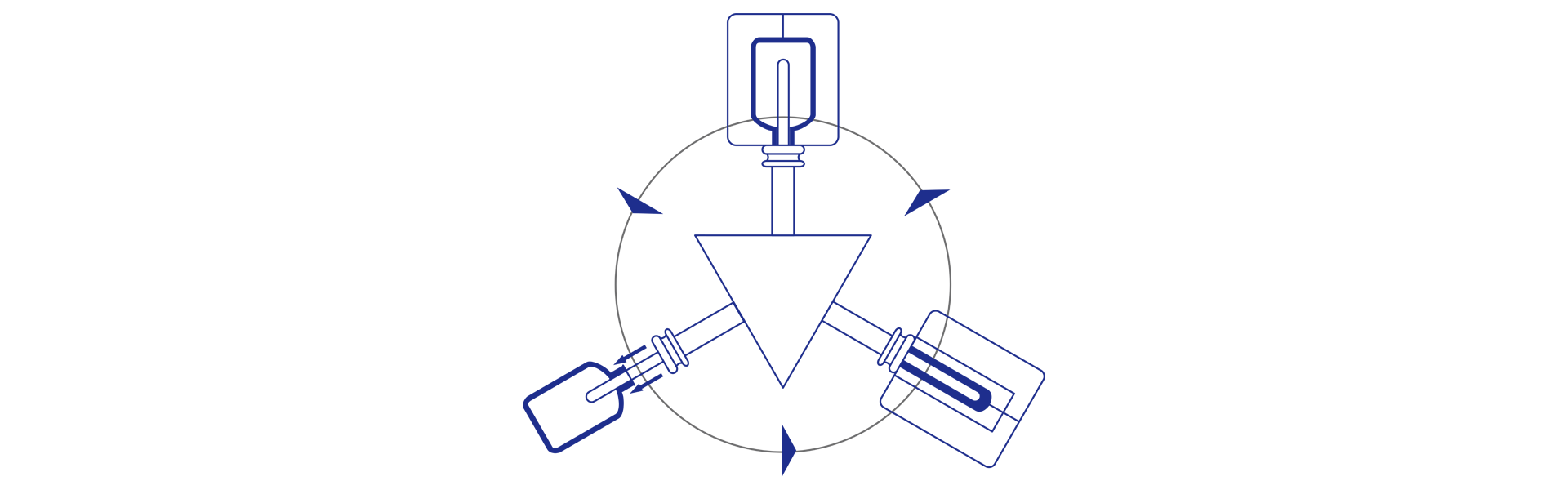
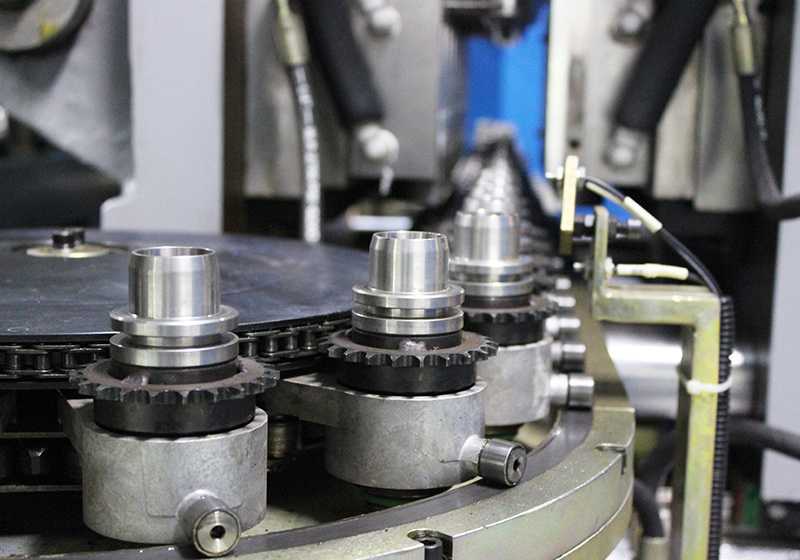
Injection Stretch Blow Molding
Firstly, the plastic raw materials are injected into the preform, which is irradiated by an infrared high-temperature lamp to heat and soften the preform body. When the optimal stretching temperature is reached, it is moved into the blow molding mold for high-pressure inflation, longitudinal stretching, blowing, cooling, shaping, and demolding.
Injecting, drawing, and blowing hollow formed products have advantages such as uniform wall thickness, good dimensional stability, light weight, and high strength.
Service Industry: Food and beverage, dairy products, candy cans, wine, daily chemical products, pharmaceuticals, health products, etc.
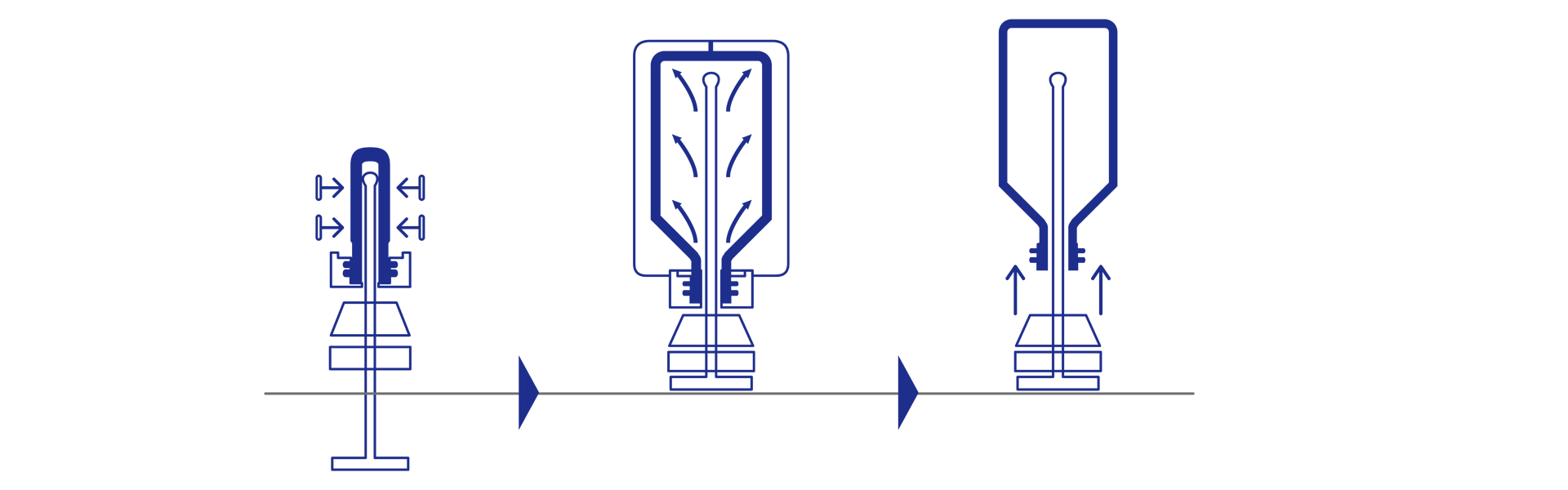
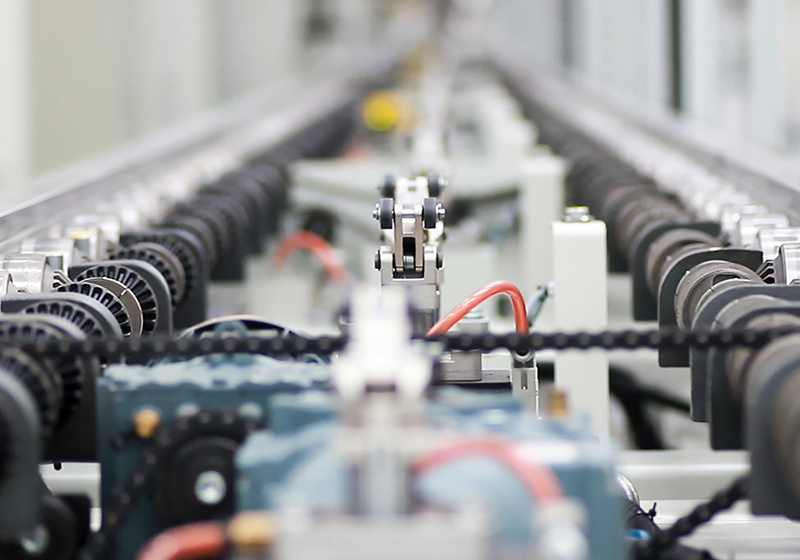
Auxiliary Processes
In order to better serve our customers, we have matched different auxiliary processes and services for different needs, including multi-color automatic printing, in mold labeling, and self-adhesive labeling.
Service Industry: Injection molded caps, buckets, boxes, injection stretch blow bottles, corresponding to food, fast-moving consumer goods, and other industries.
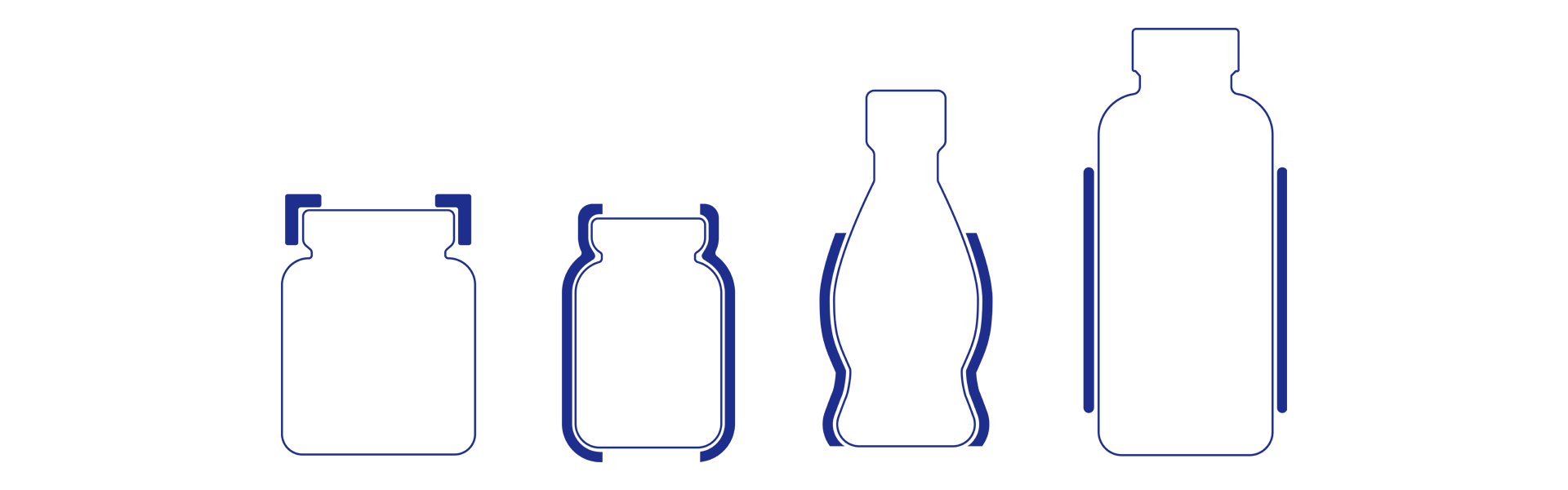